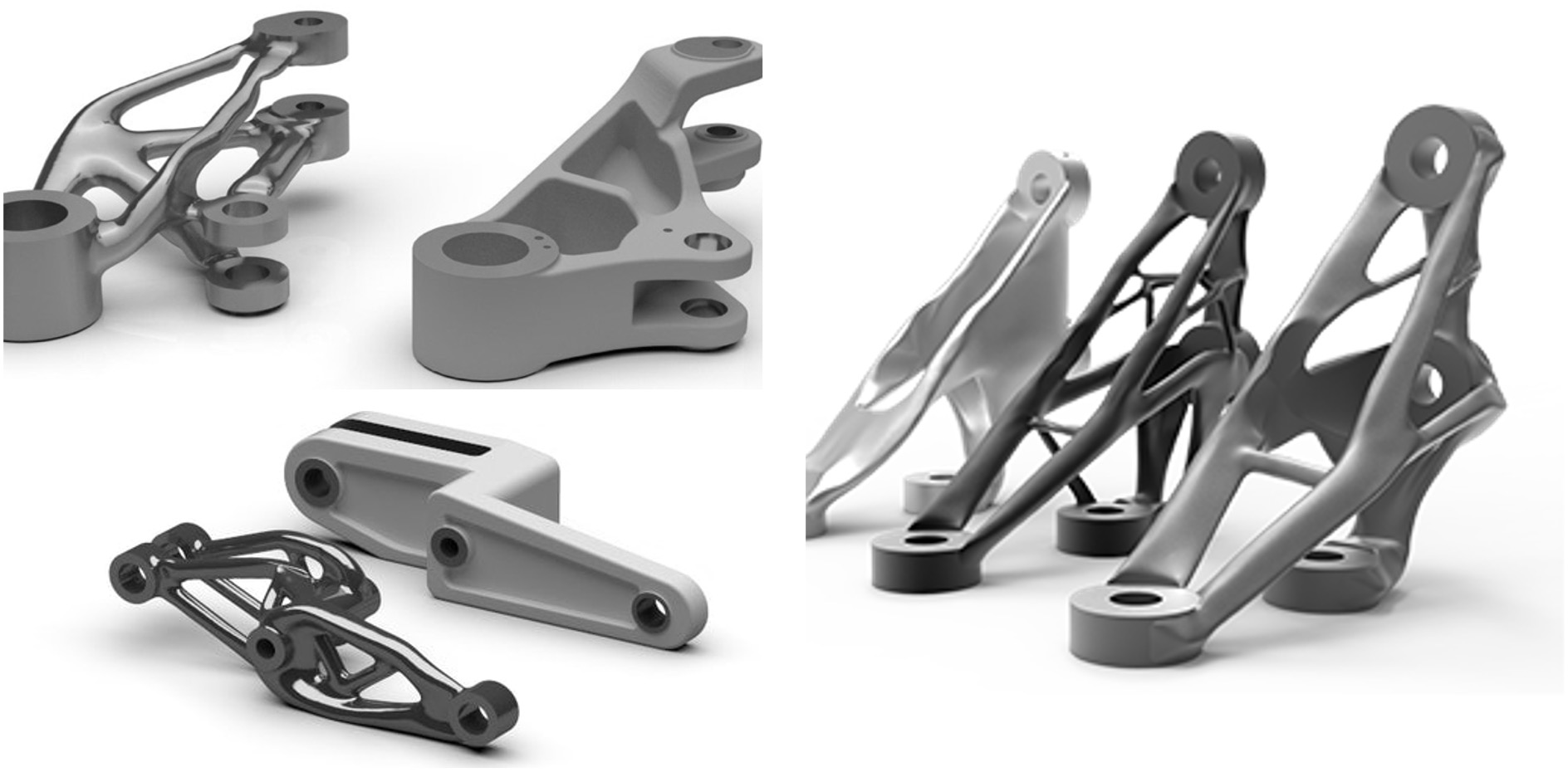
Designs are created by the designers keeping in mind the technology going to produce them. Hence the design freedom is limited to the technological capability of the manufacturing process. However, there are no such limitations when the process is additive manufacturing opening unlimited potential of the technology. Making complex shapes, lightweight parts and multi-material components are a few of the key benefits offered by AM.
Designers may face roadblocks while embracing AM because an entirely new thought process is needed while designing components for AM. Applying conventional manufacturing (CNC machining, injection molding) thought processes may not be a wise idea because both CM and AM are entirely different in their approach and considerations. Understanding the design, materials, manufacturing and post-processing are important to the success of the AM processes. Another key advantage of AM can create parts with highly optimized material allocation within the given design space.
Fabricate complex shapes
AM has the capability to create highly complex shapes with enhanced functionality which are not possible by conventional manufacturing process due to various limitations. For example, aerospace parts, strength to weight ratio is the key performance parameter. AM can create high strength complex shapes with reduced weight positively impacting the overall performance. An aeroplane can carry an extra load or could travel an extra distance saving on fuel and carbon emissions. Another example is jewellery, complex and intricate designs can only be produced by AM only. The conventional making process takes a lot of time and manual labour to create the same shape.
Complex shape design. Photo credits: nTopology
Less wastage
AM produces very little wastage since it produces parts by adding layer over layer one by one without the need for material removal. Skilled designers can create topology optimized shapes geometries that require less support or build structures resulting in significant material savings. Topology optimization software generates shapes, lattice structures and geometries that needed less material without affecting the performance and structural integrity of the component.
Ease of assembly
AM can combine multiple part assemblies into a single piece or consolidate them into fewer components. This is the greatest achievement of AM affecting almost all industries. Conventionally, parts are made individually and then assembled subsequently one by one by an operator or machine set up to create the final part. This not only increases the cost but also time to market. AM let part consolidation saves the organization from the burden of procuring large quantities, holding inventories, spare parts procurement and extra maintenance work.
Multi-material parts
Recent innovations in materials have led to the development of engineering-grade materials. Some materials like superalloys, TPU, high-performance thermoplastics are so unique to AM that they cannot be made by conventional manufacturing processes like CNC machining and injection molding. Certain high-performance materials in some cases can even substitute the metals creating lightweight a low-cost parts. Multi-material AM capability expands engineers' ability to create designs with unique properties like high insulation, conductive and non-conductive property within single geometry, high strength polymers with flexibility.
Multi-material heat exchanger. Photo credits: Aerosint
Low-cost customizations
AM can make multiple variations of the same design according to the application at almost no extra cost. Organizations can create multiple copies of the same design at speed since AM machine makes parts directly from the digital file hence lowering the cost of production. Mass production of customized design is only possible thru AM due to its unique capability from consumer durables to healthcare etc. For example, eye wears, customized eyeglass frames can be manufactured with different sizes, shapes, colours, materials according to the demand at a short notice without any investment in the tooling etc.
3D printed hand healing bandage
Minimum post-processing
AM does involve some amount of post-processing like removing build support structures, surface finishing/polishing etc. However, designers can create designs for AM that require minimum support structures and polishing depending upon application requirements. In many cases, AM build parts can be directly used for the application with base minimum post-processing and some quality checks significantly reducing the lead time. With automation taking roots in the AM process, in future, the AI-based software with automatically determine the build strategy, part orientation and support structure etc.
Conclusion
AM is slowly gaining ground however not all engineers are exposed to the various AM processes. It will take some time to come out of the conventional manufacturing-oriented design thought process. This happens with any new technology before going mainstream however devising a new AM approach will be pivotal for its success.
In future, with deeper penetration of automation in AM, the entire manufacturing process chain would be digitally connected with feedback generated at every stage. Hence, it is crucial for the industries and universities to join hands to offer specialized courses to re-skill the existing and future workforce about the different aspects of AM in order to realize its true potential across the industrial spectrum.
Blog created by - 3D SculpLab Team