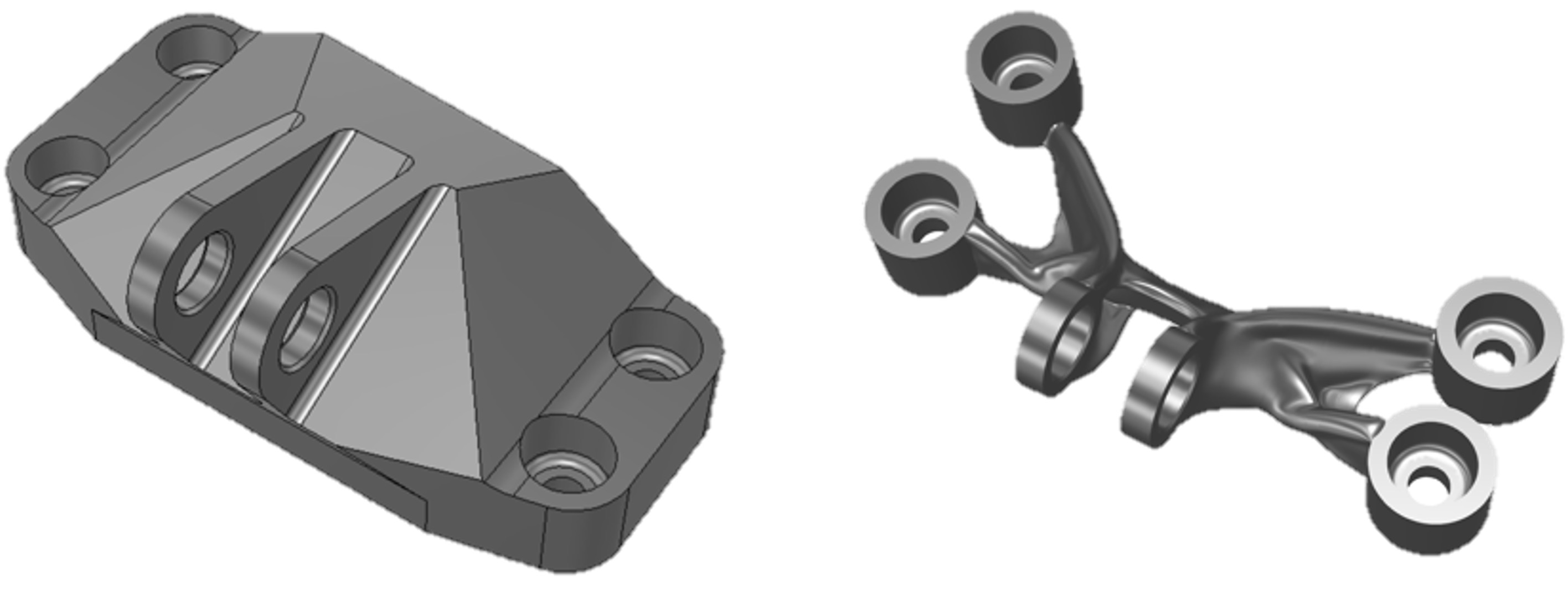
Topology optimization refers to the practice of using an iterative, software-driven process to optimize the distribution of part material within a given 3D space. It can also be considered as the computational extension of the philosophy of product design. In topology optimization, stress analysis is applied to existing part geometry. Software inputs include the location and direction of forces and stresses, fixed surfaces/mating points, a fixed design space (which may be larger than the actual part geometry), selected material and its properties, and the desired outcome.
Generative design is also like topology optimization, except original part geometry is not provided. Instead, the final part function is defined within a given design space according to similar instructions as with topology optimization (e.g. stresses, fixed locations etc.). The software then iteratively produces a series of solutions that achieve the desired performance criteria of the final part within the design space.
Generally, both approaches will create a design that is non-optimal for manufacturing, because the material is not allocated against a condition of manufacturability but instead the final part function. In addition, because each approach typically categorises the part geometry into a series of volume elements, the result may appear coarse hence Clean-up is needed for smoothing of imperfections.
Topology optimization interpreted as sacrifices in the design must be made for manufacturability. The principle is that the topology optimized shape can be maintained, and the final weight and structural properties can be closer to that of the optimized shape. Reducing the weight also means that the manufacturing costs would be less.
The desired outcome would be a specific percentage of mass reduction or optimization which requires the part to sustain the applied load irrespective of eventual part mass. Material is added and removed until a new design is created as an output. The software may create many solutions that meet the input design conditions before producing an optimized output.
Topology optimization software's
The following parameters need to be set into the software before initiation of topology optimization
Save geometry – Geometry shape is preserved during the entire optimization process and remains unchanged from start to end. At least one shape is required to be preserved to begin the process.
Interference geometry – This geometry acts as a barrier or constraint that the shape optimization process needs to go around the obstacle to generate the outcome.
Starting geometry – The user needs to define the beginning shape that the software will consider to optimize and generate the topology optimized geometry.
Fixed structures – The designer needs to define the fixed surfaces or anchor points, for example, thru-hole for fasteners. The software will keep the diameter, length or surface dimensions unchanged of fixed structures.
Load directions – Define the maximum force acting in the respective directions. During the optimization, the software will automatically create the shape around the loading point which could withstand the acting forces.
Part volume – This setting allows the designer to keep the minimum solid volume in the final optimised geometry. For example, the designer wants to keep 50% solid volume in comparison to the original shape. The software will ensure that outcome shape volume will not go below 50% of the original part.
Topology optimized BMW bike frame (Credits – BMW)
The applicability of these software tools requires that the value derived from the optimized design (for example weight reduction) justifies the cost of the production of the parts. Using conventional manufacturing process(CNC), many objects designed in this fashion would not be manufacturable or would require multi-part assemblies that would create failure points (welds, mechanical fasteners etc.) that would require additional engineering and weight addition to the finished part. That AM enables complex geometries is the key determinant for why generative design approaches have increasingly found successful applications across diverse sets of industries example aerospace, automotive and healthcare etc
Most AM processes still require post-processing, and for most metal applications, this post-processing is done using conventional methods. Therefore, that AM may produce a complex geometry more easily than a conventional method does not necessarily mean that all generatively designed geometries should be produced. Instead, AM requires a skilled designer, one who is familiar with the design rules of the selected AM process, to merge the output of a generative program with the limitations of the AM process or the constraints of post-processing.
Conclusion
AM enabled topology optimization has taken the design optimization to newer heights. It has given the designer the freedom to create shapes or designs which are usually impossible to make thru conventional manufacturing. The only drawback is that these highly optimized shapes could only be produced by AM for specific or low volume applications such as the aerospace, medical industry or highly customised product.
Blog created by - 3D SculpLab Team