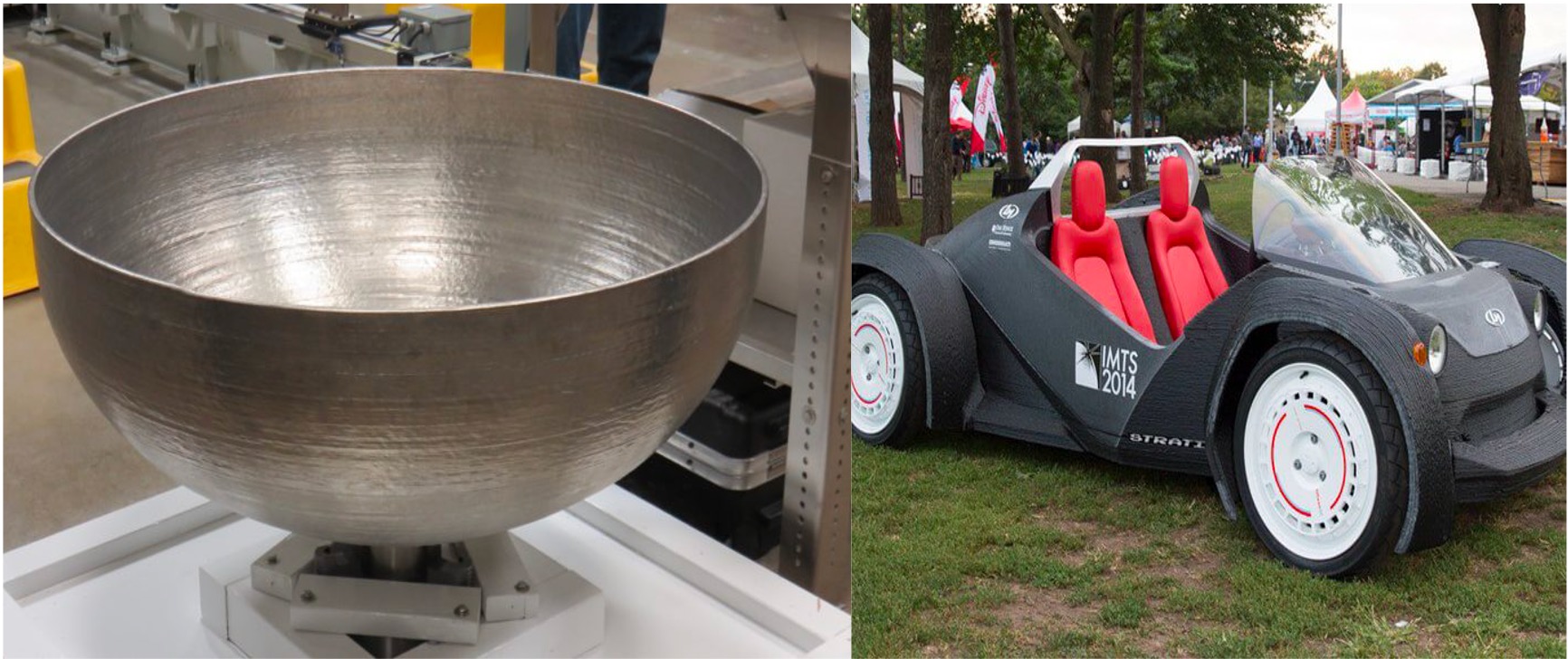
What is large format AM?
Currently available 3D printers are designed for making smaller parts used in automobiles, jewellery, aerospace etc. However, in the past few years, we’ve seen the advent of large-scale 3D printing of parts more than the one-meter size to tens of meters. Large-format additive manufacturing is one of the technologies to overcome the manufacturer's constraints regarding the production of large-size components. Parts of considerable size such as space rockets are large, heavy and complex in design and needed large manufacturing toolings and holding fixtures for production. Resulting in longer manufacturing lead times and higher production costs.
Additive manufacturing could come to the rescue of the manufacturers while producing large-size components at much lesser cost & faster lead time. The key advantage of additive manufacturing is that it can easily create objects of complex geometrical designs without the additional requirements of extra fixtures and tooling leading to lightweight structures, simplifying the assembly process and improving product performance.
Various large-format printers
BAAM (Big Area Additive Manufacturing)
BAAM system is one of the early AM machines available commercially developed by Oak Ridge National Laboratory in partnership with Cincinnati Inc USA. It's an FDM/FFF type 3D printer capable of printing large-size (up to 6x2.4x2m) objects in thermoplastics like ABS, PLA, polycarbonate, PEEK etc and at a faster rate. It has an extruder mounted on a large gantry which locates the extruder nozzle in x, y & z directions. Automotive parts, furniture items, cement casting molds and other large-scale public art could be created with this printer.
LSAM (Large Scale Additive Manufacturing)
LSAM is another polymer-based large format additive manufacturing system offered by thermwood based on FFF/FDM type extrusion process. It creates part in near net shape which can be machined to its final desired shape by the 5-axis CNC router mounted within the printer creating a sort of hybrid manufacturing system with a build volume is about 10x40 feet. LSAM could speed up part production rate than conventional manufacturing processes and can make production fixtures, molds, toolings etc.
Photo credits: Thermwood
BigRep
The BigRep machine is the cheapest available large format FDM/FF-based 3D printer in the market. It can print parts up to the volume of a one-meter cube and costs about 40~50K USD. This machine sits between the commonly available desktop FDM/FFF machines and large expensive industrial-grade 3D printers. It could be used to create parts for small cement molds, holding fixtures, creative art, furniture etc.
(WAAM) Wire Arc Additive Manufacturing
WAAM is the DED (Direct Energy Deposition) process of making large-size metal components in near net shape which can be machined to achieve the final design shape. An electric arc is used as a heat source instead of a high-intensity laser beam like other DED processes. The part is built over a base plate layer by layer controlled by a robotic arm and the part is separated from the base by a wire cut. Its capability to make near-net shape parts with complex shapes, tools, and dies could significantly reduce the overall cost of product manufacturing lead time, enhance product performance, and efficiency and reduce inventory costs.
Typical WAAM set-up. Photo credit: TWI
Large-format sand printing
Voxeljet manufactures large-size 3D printing machines to print three-dimensional geometries of sand. The printer uses binder jetting additive manufacturing technique which binds the sand particles together to unravel the design up to the size of 4x2x1 meters. Sand molds for metal castings are one of the main applications of the technology since it produces large-size molds faster and cost-effectively.
Large-scale sand printer. Photo credits: Voxeljet
Large-format concrete printing
Tvasta an India-based construction startup created the nation's first 3D-printed house built in just 21 days. The individual building parts were 3D printed at an off-site location and then transported to the pre-selected location for final assembly. Concrete 3D printing is particularly beneficial for the construction industry to create structures in less time and in a cost-effective manner. This technology opens new opportunities not only for making houses but other civic structures such as bridges, public art and other civic facilities used by the general public.
3D printed house. Photo credits: Tvasta
Applications of Large format AM
Automobile & Aerospace
Large format AM, both polymer and metal, has immense potential for aerospace and automobile industries by producing large-size components at a quicker pace and cost-effectively. Resulting in a simplified supply chain, less complex manufacturing set-up, and ease of assembly. Higher fuel economy could be achieved due to topology-optimized low-weight structure.
3D-printed rocket parts. Photo credit: Agnikul
Marine industry
The ability to print large structures cost-effectively would greatly benefit the overall marine industry. Since the marine industry is made-to-order type manufacturing where no two designs are the same. Many different types of designs could be built easily build with ease.
Construction industry & public arts
Just imagine the benefit of constructing a house or building in a matter of hours/days instead of months. The dream of affordable housing for every once could be realized only by the way of additive manufacturing. It could massively reduce the overheads and takes away the unnecessary cost burden from the construction industry. Additionally, the printed house is sturdy enough to withstand various natural calamities. Beautiful public art structures could also be created and installed at locations for site enhancement or for public viewing.
3D printed architecture. Photo credit: Worldarchitecture
Advantages
- Light weight topology optimized structures
- Reduced number of fixture & tooling set-ups
- Reduced overhead costs for large-scale projects
- Large-scale components could be created in one go
- AM machines available both in polymer & metal materials
- On-site additive manufacturing potential by mobile production set-ups
- Less manpower is needed than in conventional manufacturing processes
- Could create even larger designs beyond machine capability by creating & assembling individual components
Limitations
- Expensive equipment
- Limited material options in very large-scale AM
- Complex & expensive post-processing due to large size parts
- Additional surface treatment is needed for better surface quality
Conclusion
Currently, large-format additive manufacturing is limited to a few machine manufactures. Applications are limited to experiment basis in sectors like the automobile and construction industry. Aerospace is the only sector to fully utilize the benefits of large-scale AM successfully. Since large-scale AM systems are very expensive, organizations want to try them out initially, and then determine the right product applications. The automobile industry is one of the industries having the highest potential of leveraging the advantages of large format additive manufacturing. Large format AM could also benefit the foundry industry by printing patterns, dies & cores at lower costs and fast turnaround time. Large format AM could also address the problem of the shortage of skilled personnel in certain areas like mold making and pattern making etc.
Future work
- There’s a reluctance within the industry to embrace large-format AM due to the lack of proven application cases
- The cost of a large format AM machine is prohibitively high and not everyone could afford it. Hence, cheaper options should be made available which is well within the reach of small-scale industry
- Efforts to increase the material options catering to a wide industrial spectrum drive the large format AM growth.
- Manufacturing service provider 3DSculpLab can help small scale industry realize the benefits of large format AM without owning it
Blog created by - 3D SculpLab Team
Cover image source - Lockheed Martin and Local Motors