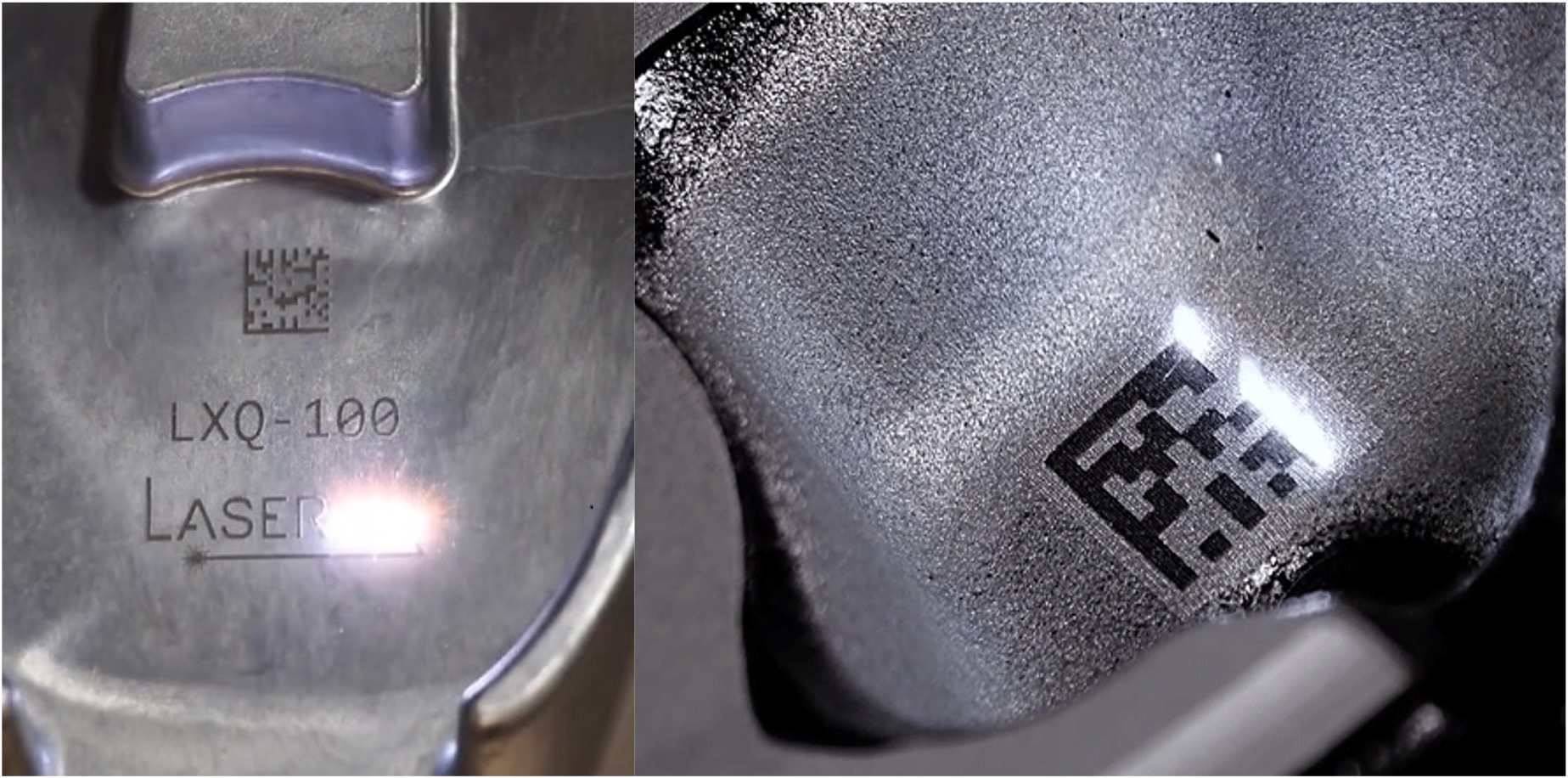
What is laser marking?
In the laser marking process, a focused laser light beam is projected on a surface creating permanent markings that doesn’t disappear for a long time. Laser marking is the most cost-effective and faster way of creating marking than other technologies.
Any type of surface is compatible be it wood, plastic, metal, ceramics, glass etc. giving a wide range of options to the manufacturers for making innovative products. However, choosing the right laser system is essential for the desired output. Fibre and Co2-based lasers are the most widely used laser system across the industry for markings. One can manipulate the output power and other specifications to suit the application requirements for the best results.
The main advantage of laser marking is that there are very few moving parts, entirely contactless, no harmful emissions of residue or vapours, and no storage of chemicals or raw materials are needed. The entire marking process is automated without manual operator intervention for machine operation, hence less manpower cost. Laser markings are generally used for engraving certain key information on a part like part number, warning note, manufacturing date, sequence number or some logos or images. Bar code could also be engraved directly on the part for the ease of trackability right from the beginning of the production till the quality control process. Barcode helps retrieve key information from the electronic manufacturing system for quick redressal. Automobile, aerospace, metal works, plastic molding and other manufacturing industries excessively use laser markings for various components. Safety critical items always have laser-engraved critical information useful to the end user.
Laser marking process
How does laser marking work?
The electrons from the laser source are charged up by applying electricity which releases the stream of energizing photos. The high-intensity amplified light strikes the target surface altering its surface properties. The laser aiming is done by the pairs of mirrors to direct at the desired location and surface creating a high-quality mark which is easily recognizable by humans or machines. Different laser types could be used to create impression on the surface, under the surface or deep into the surface or by removing the coatings on a surface.
Different types of laser markings systems
Laser marking systems depend upon the type of applications they are exposed to and the functioning of the laser system. As we know, certain materials emit light beams of different wavelengths upon atomic excitation by an external source. Like solid-state laser crystals which emit light source of wavelength around 1.064microns. Various materials emit wavelengths of different sizes so do their applications. For marking metals, fibre-based lasers are used and for polymer-type materials(rubber, plastics) CO2 lasers are used. Laser systems emit energy in continuous waves or pulsed lasers and can use either of them depending upon the application. Continuous beam laser emits energy at a constant rate while pulsed laser emits a beam in pulses at a set rate. Pulsed rate laser delivers higher energy output because they are charged up initially before emitting. Pulse rate lasers are suitable for applications with deep markings or quick marking processes. On the other hand, pulse lasers are useful for laser metal cutting, and welding applications where continuous high-intensity beam is desired.
Advantages of laser markings
- The initial investment is high for a standard set-up than other comparable processes but over a long period of time, it offers a good return on investments.
- Probably the fastest marking process and could create high visibility bar codes, QR codes and other logos etc. in seconds
- The entire process is contactless and the safest process. The entire set-up is enclosed with almost zero exposure to the operator. However, prescribed safety equipment is necessary for the operator according to the type of laser apparatus.
- Laser marking is mostly used to make marking for traceability of a product like manufacturing date, product type etc. and its child parts if sourced from outside vendors. High contrast permanent mark is created which is either machine or human-readable and can tolerate harsh environmental conditions for a long time.
- No buying and storage of special chemicals are required.
- No special preparation for the job is needed. Job is directly placed under the marking machine which is either manually or computer programmed to complete the process.
Applications of laser markings
- Markings of die-cast products
- Laser engraving on metal
- Laser marking on the lead
- Die-cast raw material marking
- Polymer laser markings
- Automobile components markings
- Textile laser marking
Markings of die-cast products
Legible marks are created on die-casting products for record keeping and trackability and are machine-readable.
Laser engraving on metal
Metal laser engraving creates deep patterns after carving the surface out. Those patterns do not get erased easily by sandblasting, chemical itching etc. Stainless steel, aluminium, titanium etc are some of the metals on which laser engraving could be applied.
Laser marking on the lead
Softer metals like lead could also be marked with detailed information part number, some alphanumeric detail or date and a bar code.
Die-cast raw material markings
Die-casting raw material markings are quite difficult by conventional means and do not last long due to uneven surface profiles. However, lasers can do this job with ease and cost-effectively. Also, laser markings have a long life.
Polymer product's laser markings
Laser marking is the best and most cost-effective solution for marking polymer-based products. No other technology will match the quality of markings created by the lasers.
Automobile components markings
Parts trackability is the most important factor in the entire automotive supply chain right from the die castings raw martial to the finished products. It's helpful in root cause analysis for any failure in the field. Just by scanning the bar code or part number, the entire supply chain history could be retrieved in a matter of seconds. It is mandatory to have traceability markings on safety critical components like airbags, seat belts etc. Laser-based marking solutions are the most efficient solution for the automobile industry where high part complexity and high-volume productions are the norms of the day.
Textile laser marking
A faster and more cost-effective method of creating a design on any fabric material.
Conclusion
Laser marking is a versatile technology in use for many decades and will continue to do so for a long time in future. It is the most economical way of creating and engraving an image, and legible information on metal as well as nonmetal objects across a wide industrial spectrum. Earlier, the size of the system was large & bulky and was mounted at a single location. Nowadays, we have compact portable handheld systems adding flexibility in handling and making it more mobile. Modern laser systems consist of multiple laser beam emitters which execute in less time than conventional laser set-ups. In future, we may see the engraving/marking done in one go by projecting the entire image cross-section on the target surface significantly reducing the processing time.
Blog created by - 3D SculpLab Team