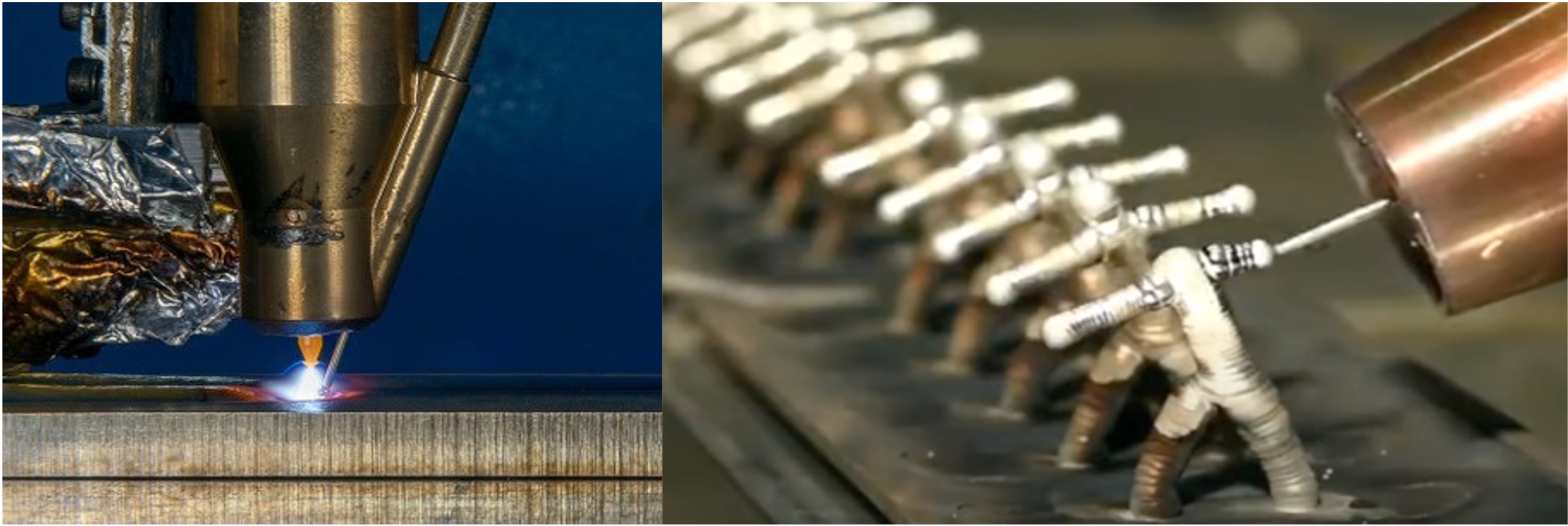
Wire arc additive manufacturing was first patented in 1920 and is one of the less discussed technology across the engineering fraternity but harbours large potential in wide-scale additive manufacturing across the industrial spectrum. WAAM is basically a DED (direct energy deposition) process capable of producing large-size parts and repairing worn-out parts & damaged components. Its capability to make near-net shape parts with complex shapes, tools, and dies could significantly reduce the overall cost of product manufacturing lead time, enhance product performance, and efficiency and reduce inventory costs. The advent of CAD/CAM software made it possible to create parts by way of additive manufacturing with a surface resolution of around 1mm and a material deposition rate of up to 10kg per hour or more.
WAAM 3D printed part. Photo credit: Norsk Titanium
How WAAM works?
Since WAAM is more closely related to direct energy deposition, the process functions by the way of melting and depositing the metal wire like arc welding. An electric arc is used as a heat source instead of a high-intensity laser beam like other DED processes. The part is built over a base plate layer by layer controlled by a robotic arm and the part is separated from the base by a wire cut. The wire is extruded from the centre of the nozzle and deposited on the plate in the form of beads which sticks together to form a part. WAAM equipment includes robotic or machine tool equipment, a build plate, CAD/CAM computer program to control the tool/robotic path, and feedstock wire. A large range of materials can be used for the WAAM process be it copper, mild steel, stainless steel, nickel alloys, aluminium alloys, titanium alloys or any other material which can be welded.
WAAM process. Photo credit: ResearchGate
Advantages of WAAM
- Large-size metal parts - WAAM has the capability to produce large-size metal parts in comparison to SLS/SLM technologies which make small-scale parts with a high-quality finish. More degree of freedom is available since a robotic arm is used for producing WAAM parts without any size limitations up to the maximum reach of the arm.
- Low production costs & materials - Since WAAM is based on the existing arc welding process, the overall cost of production and logistics is much lower than other AM technologies. WAAM feedstock is the wire which is easier to handle than powder-based raw material. Also, the process equipment can be bought off the shelf which costs lower than many industrial-grade AM systems available in the market.
- High-quality parts - WAAM-made parts possess strong mechanical characteristics and high density. These parts can be compared with parts made from other conventional manufacturing like CNC machining, and casting because the feedstock wire is fully dense therefore less chance of porosity in the fabricated parts.
- Repair and maintenance - WAAM is the most suitable technology for damaged part repairs, mold rectification, extra feature addition on existing parts etc. Also, a cost-effective way of restoring parts without the need of making new replacement parts from scratch.
- Hybrid production capability - Combining WAAM with other conventional manufacturing like CNC or hybrid manufacturing will provide designers additional design freedom to create complex shapes.
- Multi-material capability - WAAM provides additional flexibility to combine multilateral products unlocking the potential to create unique products which are generally impossible to create using conventional manufacturing.
Typical WAAM set-up. Photo credit: TWI
Constraints of WAAM
- Poor surface finish - WAAM makes near-net shape parts with poor surface quality. Parts need to be CNC machined to get the desired shape and surface finish quality.
- Set-up shielding - Some materials may like titanium needs inert gas shielding for optimal manufacturing conditions. This requires an enclosure to be created around the manufacturing set-up increasing the overall cost of manufacturing and, restricting the size of the part that can be made.
- Residual stresses - Internal stresses are introduced in WAAM-made parts due to high heat application which is a common problem in other metal 3D printing processes. So, it is essential to remove those stresses to avoid failure during application. Heat treating the part inside a furnace eliminates residual stress build-up.
Applications of WAAM
- Marine industry - WAAM is the most suitable for producing large-scale parts cost-effectively and in less time to repair or rebuilding broken parts, machine equipment etc. The marine industry can greatly benefit from this technology for the equipment under maintenance. There are a few start-ups that are trying to create small boats probably larger ships in future using this technology.
- Aerospace - Aerospace could be the biggest beneficiary of WAAM because complex, lightweight, topology-optimized geometry could be created at a fraction of the cost and time. WAAM could also enable designers to visualize efficient designs having a positive impact on fuel economy and the environment.
- Automobile - Similar to aerospace, the automobile industry could also benefit from the advantages of WAAM by creating lightweight structures resulting in improved fuel economy and fewer tailpipe emissions. Also, longer range advantage for electric vehicles.
- Medical - WAAM could provide low-cost options for titanium implant surgeries by creating custom implants at a much lower cost than other Additive manufacturing technologies like SLM which is powder bed based.
- Architecture & public utility - WAAM could enable the creation of large-size metal-based public arts and utility structures such as small bridges etc which can be installed anywhere in public places.
3D printed near net shape part. Photo credit: WAAM3D
WAAM Printers
Company Name |
Printer Name |
Location |
MaxQ |
Netherlands |
|
Merke IV |
Norway |
|
M1 |
Netherlands |
|
Arcemy |
Australia |
|
Addilan V0.1 |
Spain |
|
Arc40X, Arc60X |
Germany |
|
RoboWAAM |
UK |
Conclusion
WAAM has the capability to transform manufacturing for medium to large-scale products for certain industries by producing complex parts at a fraction of the costs. A designer can leverage topology optimization and even multi-material parts are possible by WAAM. Combining WAAM with existing machining set-ups will provide additional manufacturing flexibility and can produce geometries not possible with conventional manufacturing. WAAM creates near-net shape parts with surface quality not so good hence proper machining is needed to bring it to the required dimensional tolerances and surface finish specifications. Stock size can be as low as 1mm resulting in maximum material utilization from small size to bigger size parts resulting in less wastage and lower overall cost of production. Usages in industries like aerospace, automobile and medical will reduce product development costs and delivery time, positively impacting their bottom lines.
Blog created by - 3D SculpLab Team