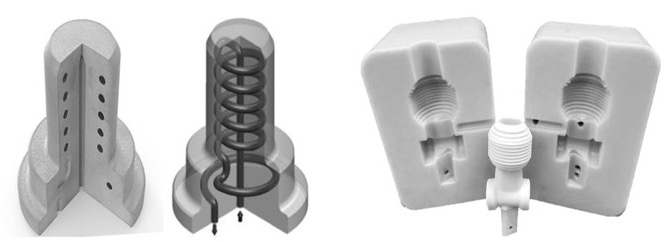
Overview
AM is slowly locating its space inside the manufacturing industry to enhance the performance and productivity of tooling's made by conventional manufacturing. AM could be used to create proto tooling for design validation or short-run productions. AM based tooling can greatly help the industry in cutting development time and time to market. In the following article, we’ll discuss the advantages of using AM in injection molding.
Speed
Proto mold could be created in a matter of hours and can be put to use in a short time. Fast, multiple iterations is possible without the need for an actual mold. The digital fabrication tools needed for AM to produce mold tooling result in lesser production steps though complicated in nature.
Cost
AM based mold tooling fabrication is generally more cost-effective than conventional manufacturing for prototyping. CM made toolings takes a lot of time to fabricate and costs much higher than AM. There’s very less scope of iterations in CM enabled tooling’s than AM due to cost and time factors. While there is no such limitation in AM enabled tooling’s. A designer could do multiple iterations at a fraction of the cost and a smaller lead time.
Performance
In injection molding, the production rate is determined is from how quickly the heat is extracted from the plastic part after injection. The injection happens in 100 milliseconds or less but the cooldown takes a much longer time. Conventionally, cooling channels are created by multiple steps of drilling operations, plugging of holes to facilitate the machining operations. These channels cannot be placed closer to the core/cavity surface due to limitations of the conventional manufacturing process, resulting in non-uniform distribution of heating and cooling effect on mold surface. The advantage of AM is it can generate a complex web of embedded cooling channels parallel and closer to the core/cavity surface in any shape without the need of a conventional manufacturing setup. This results in an even distribution of heating and cooling effects, significantly reducing cycle time and warpage related rejection.
Conventional and conformal cooling channels Photo credits: LinearAMS
AM enabled low volume production mold tooling, often at a less price and reduced lead time as if the tool is carved out of the metal block. There are many fitting processes for this requirement such as the Polyjet AM and SLA of the composite materials usually resin with carbon fibre. AM can also be used to fabricate high-performance metal tooling’s that can operate over a large number of cycles. Conformal cooling channels is an excellent option in many cases within the mold to enhance performance and increase the rate of production.
Secondly, downtime due to breakdown is quite common across the manufacturing industry and sometimes it takes a lot of money and time to fix it. Here, AM could rescue the industry from the loss of time and money. If the mold is inactive due to a broken part, it can be quickly repaired or replicated easily by 3D printing in a matter of hours at a fraction of cost. Conventionally, it could have taken a few days to fix the breakdown.
Conclusion
AM enabled complexities could create complex patterns for casting, mold cores, conformal cooling channels within the mold core for a uniform cooling pattern across the mold and faster cycle time. AM-enhanced mold tooling has led to the development of dedicated metal AM machines for the fabrication of mold tooling. Because the internal and external surfaces of the mold frequently needed a very smooth surface finish, along with features such as deep and restricted cavities, it is favourable to combine both AM and machining.
Blog created by - 3D SculpLab Team