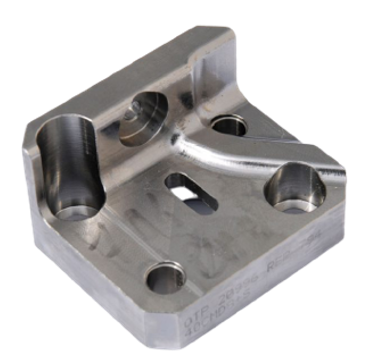
Wide material options for your requirements
Aluminum 6061 is an extremely popular alloy, excellent for jobs that require forming or welding. It is the most commonly available aluminum alloy and provides a clean surface finish. Unlike other aluminum alloys, 6061 has high corrosion resistance. It can be forged, hot worked, and readily welded, as well as heat treated, annealed, and aged. It anodizes well and provides a bright, colourful finish.
Al 6061 | Al 6061-T6 (Hardened) | |
Temper | - | T6 |
Modulus of elasticity / Young Mod. | 68 GPa | 68 GPa |
Yield Strength | 55.2 MPa | 276 MPa |
Ultimate Tensile strength | 124 MPa | 310 MPa |
Elongation at break | 25% | 12 - 17% |
Hardness | 30 HRB | 60 HRB |
Max Working temp. | 130 - 150˚C | 130 - 150˚C |
Thermal expansion coefficient | 23.6 µm/m-°C | 23.6 µm/m-°C |
Thermal conductivity | 180 W/m-°C | 167 W/m-°C |
Electrical resistivity | 3.6 μΩ-cm | 3.9 μΩ-cm |
Corrosion | High Resistance | High Resistance |
Welding | High weldability | High weldability |
Price | TBD |
Lead Time | ~5 days |
Max part size | 500x500x500mm |
Disclaimer - Material properties are for general-purpose reference only and have been made available on a best effort basis for the users as a quick information guide for the material selection.
Aluminum alloy 7075 is the strongest of available aluminum alloys with zinc as a major element, excellent for jobs that require extreme strength while remaining lightweight. It possesses great cracking resistance and can be forged and heat-treated but is not ideal for welding. 7075 can be heat treated, annealed, and aged. It is not as ideal for anodizing compared to Aluminum 6061 and may produce a yellowish tint when clear anodizing.
Temper | T6 |
Modulus of elasticity / Young Mod. | 71 GPa |
Yield Strength | 503 MPa |
Ultimate Tensile strength | 572 MPa |
Elongation at break | 11% |
Hardness | 87 HRB |
Max Working temp. | 100˚C |
Thermal expansion coefficient | 23.6 µm/m-°C |
Thermal conductivity | 129 W/m-°C |
Electrical resistivity | 5.15 μΩ-cm |
Corrosion | Moderate Resistance |
Welding | Poor Weldability |
Price | TBD |
Lead Time | ~5 days |
Max part size | 500x500x500mm |
Disclaimer - Material properties are for general-purpose reference only and have been made available on a best effort basis for the users as a quick information guide for the material selection.
Aluminum alloy 2024 is an exceptionally high mechanical strength alloy, suitable for parts that require more strength while remaining lightweight. It also has excellent fatigue and cracking resistance, making it a desirable material for automotive & aircraft components. Aluminum 2024 can be machined to a high finish. It can be forged and hot worked but is not ideal for welding or soldering. 2024 responds well to heat treatment, annealing, and tempering. It can be anodized but results in a darker and less corrosion-resistant finish than Aluminum 6061.
Temper | T6 |
Modulus of elasticity / Young Mod. | 74 GPa |
Yield Strength | 345 MPa |
Ultimate Tensile strength | 427 MPa |
Elongation at break | 5% |
Hardness | 78 HRB |
Max Working temp. | 190˚C |
Thermal expansion coefficient | 23.2 µm/m-°C |
Thermal conductivity | 151 W/m-°C |
Electrical resistivity | 4.49 μΩ-cm |
Corrosion | Poor Resistance |
Welding | Good Weldability |
Price | TBD |
Lead Time | ~5 days |
Max part size | 500x500x500mm |
Disclaimer - Material properties are for general-purpose reference only and have been made available on a best effort basis for the users as a quick information guide for the material selection.
MIC6 Cast aluminum tooling plate offers superior dimensional stability and flatness compared to 6061 rolled plates. Being a cast product, it possesses very low internal stresses. Fully stress-relieved, Mic6 is a free-cutting aluminum alloy with excellent machining characteristics. Additionally, it is lightweight, smooth, and free from tension, contaminants, and porosity.
Modulus of elasticity / Young Mod. | 71 GPa |
Yield Strength | 105 MPa |
Ultimate Tensile strength | 165 MPa |
Elongation at break | 3% |
Hardness | 65 HB |
Max Working temp. | 400˚C |
Thermal expansion coefficient | 23.6 µm/m-°C |
Thermal conductivity | 142 W/m-°C |
Electrical resistivity | 4.79 μΩ-cm |
Corrosion | Good Resistance |
Welding | Good Weldability |
Price | TBD |
Lead Time | ~5 days |
Max part size | 500x500x500mm |
Disclaimer - Material properties are for general-purpose reference only and have been made available on a best effort basis for the users as a quick information guide for the material selection.
Copper alloy 110 is an extremely popular copper alloy, with a wide range of applications due to its high corrosion resistance, conductivity, and finish. It has the highest electrical conductivity of any metal, except silver. When exposed to the elements, it forms a thin protective patina that is relatively impermeable. Copper 110 is ideal when extensive machining is not required, as it has extremely low machinability compared to other copper alloys. It is excellent for hot and cold forming, as well as soldering. Copper 110 is not easily welded or brazed.
Temper | Annealed |
Modulus of elasticity / Young Mod. | 117 GPa |
Yield Strength | 283 - 345 MPa |
Ultimate Tensile strength | 296 - 359 Mpa |
Elongation at break | 3 - 16% |
Hardness | 57 HRB |
Thermal expansion coefficient | 17.6 µm/m-°C |
Thermal conductivity | 390 W/m-°C |
Electrical resistivity | 1.76 μΩ-cm |
Welding | Moderate Weldability |
Price | TBD |
Lead Time | ~5 days |
Max part size | 500x500x500mm |
Disclaimer - Material properties are for general-purpose reference only and have been made available on a best effort basis for the users as a quick information guide for the material selection.
Copper alloy C101 is the designation for moderate copper used in engineering applications. High ductility and impact strength also serve to make an extremely useful material. Copper alloy C101 is also known as HC or high conductivity copper and also has high thermal conductivity. Copper alloy C101 is, therefore, the material of choice for use in conductors and electrical components. It has a very high percentage of Copper in it - 99.9%.
Modulus of elasticity / Young Mod. | 115 GPa |
Yield Strength | 69 - 365 MPa |
Ultimate Tensile strength | 221 - 455 MPa |
Elongation at break | 55% |
Hardness | 75 - 90 HV |
Thermal expansion coefficient | 17 µm/m-°C |
Thermal conductivity | 383 - 391 W/m-°C |
Electrical resistivity | 1.74 μΩ-cm |
Corrosion | Good to excellent |
Welding | Poor Weldability |
Price | TBD |
Lead Time | ~5 days |
Max part size | 500x500x500mm |
Disclaimer - Material properties are for general-purpose reference only and have been made available on a best effort basis for the users as a quick information guide for the material selection.
Brass CDA 360 alloy has the highest machinability of all copper alloys, extremely popular for parts that require strength, weight, or a polished surface finish. Brass 360 has a very wide range of applications and is ideal for industrial and electronic industries. Unlike steel, 360 also forms a thin protective patina that does not rust. It has fair hot forming properties and is not ideal for cold forming, welding, soldering, and brazing. Brass 360 can be forged and annealed.
Modulus of elasticity / Young Mod. | 97 GPa |
Yield Strength | 124 - 310 MPa |
Ultimate Tensile strength | 338 - 469 MPa |
Elongation at break | 53% |
Hardnes | 63 HB |
Thermal expansion coefficent | 20.5 µm/m-°C |
Thermal conductivity | 115 W/m-°C |
Price | TBD |
Lead Time | ~5 days |
Max part size | 500x500x500mm |
Disclaimer - Material properties are for general-purpose reference only and have been made available on a best effort basis for the users as a quick information guide for the material selection.
AISI 1018 mild/low carbon steel has excellent weldability, produces a uniform and harder case, and is considered the best steel for carburized parts. AISI 1018 mild/low carbon steel offers a good balance of toughness, strength, and ductility. It produces exceptional welds that do not require pre- or post-heating processes. 1018 responds well to case hardening and heat treating.
Modulus of elasticity / Young Mod. | 200 GPa |
Yield Strength | 370 MPa |
Ultimate Tensile strength | 440 MPa |
Elongation at break | 15% |
Hardness | 71 HRB |
Thermal expansion coefficient | 12.1 µm/m-°C |
Thermal conductivity | 51.9 W/m-°C |
Electrical resistivity | 15.9 μΩ-cm |
Corrosion | Poor Resistance |
Welding | High weldability |
Price | TBD |
Lead Time | ~5 days |
Max part size | 500x500x500mm |
Disclaimer - Material properties are for general-purpose reference only and have been made available on a best effort basis for the users as a quick information guide for the material selection.
Steel alloy 1045 is a versatile medium carbon alloy, ideal for parts that require strength and impact resistance. Due to its higher carbon content, it has higher tensile strength. 1045 has excellent ductility and toughness. It is not ideal for welding or forming due to its higher carbon content. 1045 responds to heat treatment extremely well, but it is not ideal for case hardening.
Modulus of elasticity / Young Mod. | 206 GPa |
Yield Strength | 330 - 580 MPa |
Ultimate Tensile strength | 606 - 682 MPa |
Elongation at break | 13 - 18% |
Hardness | 89 HRB |
Thermal expansion coefficient | 12.1 µm/m-°C |
Thermal conductivity | 51.9 W/m-°C |
Electrical resistivity | 16 - 19 μΩ-cm |
Corrosion | Poor Resistance |
Welding | Good Weldability |
Price | TBD |
Lead Time | ~5 days |
Max part size | 500x500x500mm |
Disclaimer - Material properties are for general-purpose reference only and have been made available on a best effort basis for the users as a quick information guide for the material selection.
Steel alloy 4140 cold roll is a popular general-purpose alloy, ideal for parts that require high tensile strength and toughness. It has considerable atmospheric corrosion and wear resistance, and will not become brittle. It is not ideal for welding due to its lead content. It is often used for forging, responds very well to heat treatment, and can be annealed.
Modulus of elasticity / Young Mod. | 206 GPa |
Yield Strength | 660 - 965 MPa |
Ultimate Tensile strength | 896 - 1103 MPa |
Elongation at break | 17 - 22% |
Hardnes | 97 HRB |
Thermal expansion coefficent | 12.1 µm/m-°C |
Thermal conductivity | 42 W/m-°C |
Electrical resistivity | 22 μΩ-cm |
Corrosion | Good Resistance |
Welding | Moderate Weldability |
Price | TBD |
Lead Time | ~5 days |
Max part size | 500x500x500mm |
Disclaimer - Material properties are for general-purpose reference only and have been made available on a best effort basis for the users as a quick information guide for the material selection.
Steel alloy 1215 is a popular free-machining alloy (FMA), ideal for parts that require considerable machining and a bright finish. It responds well to slight bending, threading, and nibbling, but is not ideal for parts that may be subject to very severe fatigue stress. It possesses better weldability and formability and can be heat treated.
Modulus of elasticity / Young Mod. | 200 GPa |
Yield Strength | 415 MPa |
Ultimate Tensile strength | 540 MPa |
Elongation at break | 10% |
Hardnes | 85 HRB |
Thermal expansion coefficent | 11.5 µm/m-°C |
Thermal conductivity | 51.9 W/m-°C |
Electrical resistivity | 17.4 μΩ-cm |
Corrosion | Good Resistance |
Welding | Good Weldability |
Price | TBD |
Lead Time | ~5 days |
Max part size | 500x500x500mm |
Disclaimer - Material properties are for general-purpose reference only and have been made available on a best effort basis for the users as a quick information guide for the material selection.
ABS(Acrylonitrile Butadiene Styrene) blocks can be processed with ease and versatility. They can be machined, turned, drilled, milled, sawed, bored, die-cut, routed, and sheared using high-speed cutting tools. ABS can be machine finished by filing, grinding, sanding, buffing, and polishing.
Color - Natural, black
Modulus of elasticity / Young Mod. | 1.83 - 2.21 Gpa |
Yield Strength | 31.0 - 42.7 MPa |
Ultimate Tensile strength | 15.9 - 39.9 MPa |
Elongation at break | 10 - 50% |
Flexural Strength | 34.5 - 77.9 |
Hardness | 80.0 - 105 HRR |
Max Working temp. | Upto 70˚C |
Thermal expansion coefficient | 59.4 - 101 µm/m-°C |
Price | TBD |
Lead Time | ~5 days |
Max part size | 500x500x500mm |
Disclaimer - Material properties are for general-purpose reference only and have been made available on a best effort basis for the users as a quick information guide for the material selection.
Delrin (POM-H) is a versatile low-cost plastic in the acetal family, ideal for parts that require strength and resilience while machining to very tight tolerances. It has excellent dimensional stability and friction resistance, making it long-wearing. Unlike nylon, it has a very low moisture absorption rate, making it suitable for use in wet environments.
Color - Black & white
Modulus of elasticity / Young Mod. | 3.1 GPa |
Ultimate Tensile strength | 75 MPa |
Elongation at break | 30% |
Flexural Strength | 89 MPa |
Compressive Strength | 103 MPa |
Hardness | 122 HRR |
Max Working temp. | Upto 80˚C |
Thermal expansion coefficient | 84 µm/m-°C |
Thermal conductivity | 0.360 W/m-˚C |
UV Resistance | Moderate |
Price | TBD |
Lead Time | ~5 days |
Max part size | 500x500x500mm |
Disclaimer - Material properties are for general-purpose reference only and have been made available on a best effort basis for the users as a quick information guide for the material selection.
Nylon is a versatile low-cost plastic, ideal for parts that require high compressive strength and friction resistance while machining to very tight tolerances. It can be used in place of metal in some applications, allowing for longer-wearing parts that require lower maintenance than its metal counterpart. Nylon generally is stronger, withstands higher temperatures.
Color - Black, white
Modulus of elasticity / Young Mod. | 2.76 GPa |
Ultimate Tensile strength | 82 MPa |
Elongation at break | 30% |
Flexural Strength | 110 MPa |
Compressive Strength | 103 MPa |
Hardnes | 115 HRR |
Max Working temp. | Upto 90˚C |
Thermal expansion coefficent | 90 µm/m-°C |
Thermal conductivity | 0.24 W/m-˚C |
UV Resistance | Moderate |
Price | TBD |
Lead Time | ~5 days |
Max part size | 500x500x500mm |
Disclaimer - Material properties are for general-purpose reference only and have been made available on a best effort basis for the users as a quick information guide for the material selection.
Acrylic(PMMA) has excellent weathering resistance, especially applied to outdoor, ranking the highest in other plastics, and both a good surface hardness and gloss, processing plasticity, can be made of the required shape and products. Has extremely superior optical performance. Excellent transparency, light transmission rate of 92%, and can also be safe to use outdoor.
Color - Transparent
Modulus of elasticity / Young Mod. | 3.3 GPa |
Yield Strength | 72 MPa |
Ultimate Tensile strength | 35 MPa |
Elongation at break | 5% |
Flexural Strength | 105 MPa |
Compressive Strength | 103 MPa |
Hardnes | 80 - 100 HRM |
Max Working temp. | Upto 70˚C |
Thermal expansion coefficent | 70 µm/m-°C |
Thermal conductivity | 0.19 W/m-˚C |
UV Resistance | Good |
Price | TBD |
Lead Time | ~5 days |
Max part size | 500x500x500mm |
Disclaimer - Material properties are for general-purpose reference only and have been made available on a best effort basis for the users as a quick information guide for the material selection.
Polyether ether ketone (PEEK) is a popular high-strength plastic resin, ideal for parts that require strength and stiffness. It has an extremely high resistance to heat, moisture, and chemicals and can withstand multiple cycles in hot water or steam. PEEK also performs well in ultra-high vacuum environments.
Color - Black
Modulus of elasticity / Young Mod. | 4.3 GPa |
Ultimate Tensile strength | 110 MPa |
Elongation at break | 40% |
Flexural Strength | 172 MPa |
Compressive Strength | 138 MPa |
Hardness | 126 HRR |
Max Working temp. | Upto 240˚C |
Thermal expansion coefficient | 46.8 µm/m-°C |
Thermal conductivity | 0.25 W/m-˚C |
UV Resistance | Good |
Price | TBD |
Lead Time | ~5 days |
Max part size | 500x500x500mm |
Disclaimer - Material properties are for general-purpose reference only and have been made available on a best effort basis for the users as a quick information guide for the material selection.
PTFE (Polytetrafluoroethylene) commonly known as Teflon is an extremely resilient plastic, ideal for screw machine parts that require high-impact strength and durability. It has excellent resistance to frictional wear, weathering, flame, heat, chemicals, and radiation. Teflon is not affected by the ultraviolet and is resistant to oxidation, discolouration, and embrittlement. Teflon is completely resistant to hydrolysis. Teflon is a good barrier for water permeation.
Color - Black
Modulus of elasticity / Young Mod. | 0.4 - 0.5 GPa |
Yield Strength | 19 MPa |
Ultimate Tensile strength | 20 - 34 MPa |
Elongation at break | 2 - 4% |
Hardnes | 5.9 - 6.5 HV |
Max Working temp. | Upto 260˚C |
Price | TBD |
Lead Time | ~5 days |
Max part size | 500x500x500mm |
Polycarbonate is a transparent thermoplastic material with good strength and stiffness and outstanding impact resistance. It provides the best mechanical property and electrical insulation, high dimensional stability and excellent creep resistance. Polycarbonate's toughness and optical clarity make it ideal for a wide variety of applications. And it can be used in temperatures up to +110°C.
Color - Black, White, Semi-transparent
Modulus of elasticity / Young Mod. | 2 GPa |
Yield Strength | 60 - 70 MPa |
Ultimate Tensile strength | 61 MPa |
Elongation at break | 50 - 120% |
Flexural Strength | 90 MPa |
Compressive Strength | 17.7 - 21.7 HV |
Hardnes | 77 HRM |
Max Working temp. | Upto 110˚C |
Thermal expansion coefficent | 68 µm/m-°C |
Thermal conductivity | 0.89 - 0.21 W/m-˚C |
UV Resistance | Moderate |
Price | TBD |
Lead Time | ~5 days |
Max part size | 500x500x500mm |
Polypropylene (PP) is an economical material that offers a combination of outstanding physical, chemical, mechanical, thermal, and electrical properties not found in any other thermoplastic. Polypropylene has excellent chemical resistance in corrosive environments where there are organic solvents, degreasing agents, or electrolytic attacks, but poor resistance to aromatic, aliphatic, and chlorinated solvents. It is lightweight, non-staining, and exhibits a low moisture absorption rate. It’s ideal for the transfer of hot liquids and gases, and in vacuum system atmospheres with high heat and pressure.
Color - White
Modulus of elasticity / Young Mod. | 2 GPa |
Yield Strength | 60 - 70 MPa |
Ultimate Tensile strength | 61 MPa |
Elongation at break | 50 - 120% |
Flexural Strength | 90 MPa |
Compressive Strength | 17.7 - 21.7 HV |
Hardness | 77 HRM |
Max Working temp. | Upto 110˚C |
Thermal expansion coefficient | 68 µm/m-°C |
Thermal conductivity | 0.89 - 0.21 W/m-˚C |
UV Resistance | Moderate |
Price | TBD |
Lead Time | ~5 days |
Max part size | 500x500x500mm |
Disclaimer - Material properties are for general-purpose reference only and have been made available on a best effort basis for the users as a quick information guide for the material selection.
30% glass-filled nylon is suitable for use in the automotive industry & other general engineering applications where very high strength & resistance to high temperature is key. It also provides high strength and rigidity.
Price | TBD |
Lead Time | ~5 days |
Max part size | 400x400x500mm |
Disclaimer - Material properties are for general-purpose reference only and have been made available on a best effort basis for the users as a quick information guide for the material selection.
Stainless steel 316 is the standard molybdenum-bearing grade, second in importance to 304 amongst the austenitic stainless steels. The molybdenum gives 316 better overall corrosion-resistant properties than Grade 304, notably higher resistance to pitting and crevice corrosion in chloride environments. 316L stainless steel offers higher creep, stress to rupture and tensile strength at elevated temperatures.
Modulus of elasticity / Young Mod. | 193 GPa |
Yield Strength | 170 MPa |
Ultimate Tensile strength | 485 MPa |
Elongation at break | 40% |
Hardness | 95 HRB |
Thermal expansion coefficient | 15.9 µm/m-°C |
Thermal conductivity | 16.3 W/m-°C |
Electrical resistivity | 74 μΩ-cm |
Corrosion | High Resistance |
Welding | Excellent weldability |
Price | TBD |
Lead Time | 4~5 days |
Max part size | 500x500x500mm |
Disclaimer - Material properties are for general-purpose reference only and have been made available on a best-effort basis for the users as a quick information guide for the material selection.
SS 304 is the most versatile and widely used stainless steel available. And, is machinable and has good welding characteristics. It is non-magnetic and less thermally & electrically conductive. SS 304 can be readily braked or roll-formed into a variety of components for applications in the industrial, architectural, and transportation fields. Post-weld annealing is not required when welding thin sections. SS 304L is the low-carbon version of SS 304.
Modulus of elasticity / Young Mod. | 195 GPa |
Yield Strength | 240 MPa |
Ultimate Tensile strength | 585 MPa |
Elongation at break | 50% |
Hardness | 80 HRB |
Max Working temp. | 925˚C |
Thermal expansion coefficient | 17.3 µm/m-°C |
Thermal conductivity | 15.2 W/m-°C |
Electrical resistivity | 72 μΩ-cm |
Price | TBD |
Lead Time | 4~5 days |
Max part size | 500x500x500mm |
Disclaimer - Material properties are for general-purpose reference only and have been made available on a best effort basis for the users as a quick information guide for the material selection.
SS 17-4PH is also known as Grade360. It is precipitation-hardened steel with an unmatched union of excellent corrosion resistance, high strength and good mechanical characteristics. Its multi-properties provide designers with a unique opportunity to create reliable products with simplified manufacturing resulting in lower production costs. Not suitable for anodizing.
Yield Strength | 1000 MPa |
Ultimate Tensile strength | 1103 MPa |
Elongation at break | 5% |
Hardness | 35RC |
Max Working temp. | upto 316˚C |
Thermal expansion coefficient | 10.8 µm/m-°C |
Thermal conductivity | 17.3 - 18.7 W/m-°C |
Electrical resistivity | 98 μΩ-cm |
Corrosion | Excellent |
Welding | Good |
Price | TBD |
Lead Time | 4~5 days |
Max part size | 500x500x500mm |
Disclaimer - Material properties are for general-purpose reference only and have been made available on a best effort basis for the users as a quick information guide for the material selection.